ISO 9001 Lead Auditor
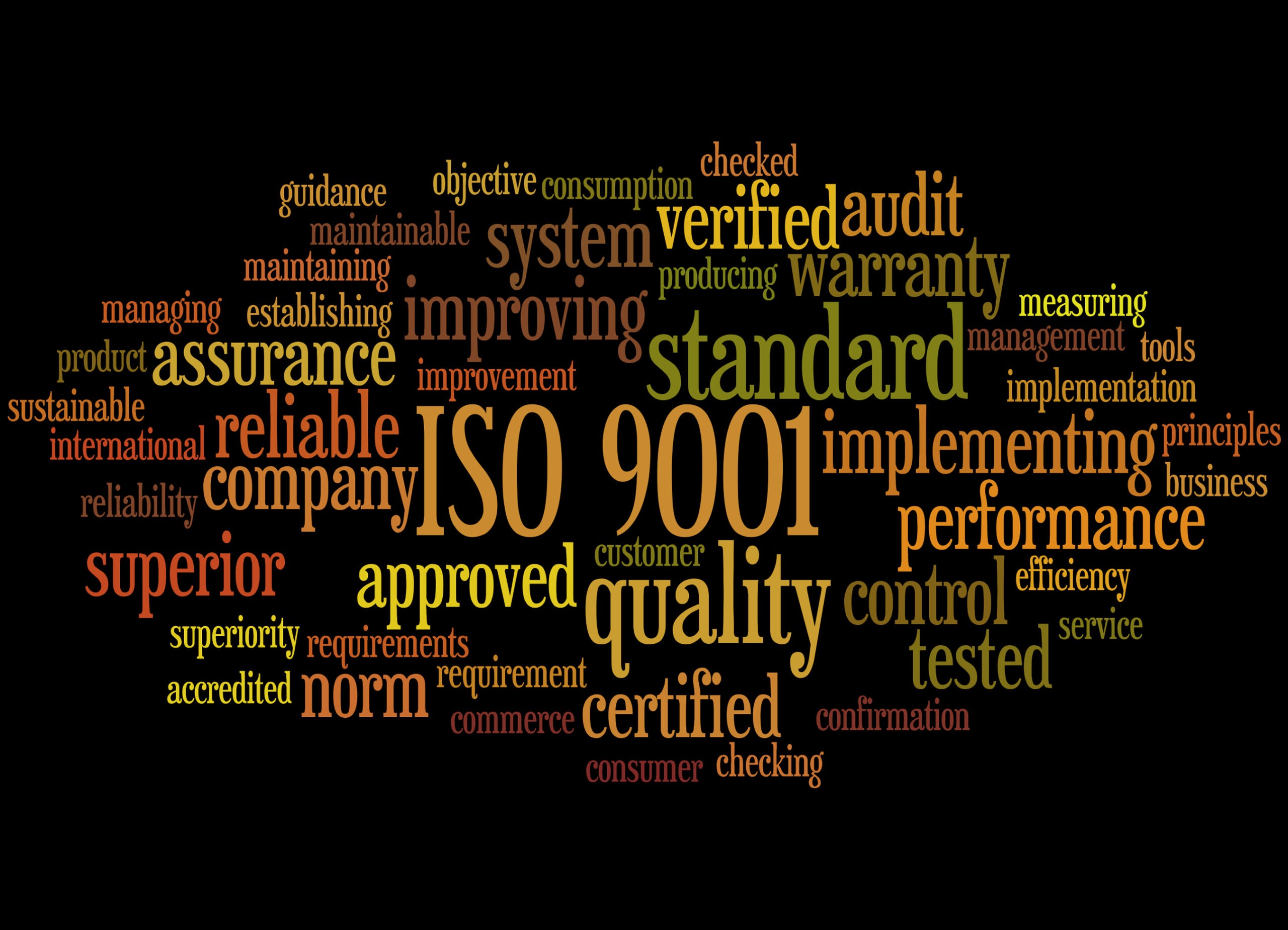
ISO 9001 is an international standard for quality management systems (QMS). It outlines a set of principles and practices that organizations can use to ensure they consistently deliver high-quality products or services to their customers. The standard is applicable to a wide range of industries and organizations, including manufacturing, service providers, government agencies, and non-profit organizations.
Key aspects of ISO 9001 include:
- Customer Focus: ISO 9001 emphasizes the importance of understanding and meeting customer requirements and expectations. Customer satisfaction is a central goal of the standard.
- Process Approach: It promotes a process-oriented approach to quality management. Organizations are encouraged to identify and define the key processes that affect quality and to continually improve them.
- Continuous Improvement: ISO 9001 encourages a culture of continual improvement. Organizations are expected to monitor and measure their processes, products, and services and take corrective and preventive actions when necessary.
- Leadership and Engagement: Top management plays a crucial role in establishing and maintaining the QMS. The standard emphasizes leadership commitment to quality and the involvement of all employees in achieving quality objectives.
- Evidence-Based Decision Making: ISO 9001 promotes decision-making based on data and evidence rather than intuition or opinion. Organizations are expected to collect and analyze relevant data to support their decision-making processes.
- Relationship Management: The standard recognizes the importance of managing relationships with suppliers and other interested parties that can affect the organization’s ability to provide quality products or services.
Achieving ISO 9001 certification involves a series of steps, including:
- Commitment and Leadership: Top management must commit to implementing and maintaining a QMS and appoint a Quality Management Representative.
- Scope Definition: Define the scope of your QMS, including the products, services, and processes that are within its scope.
- Process Identification: Identify and document the key processes within your organization that affect quality.
- Documentation: Create the necessary documentation, including a Quality Manual, documented procedures, and records.
- Training and Awareness: Ensure that employees are aware of the QMS and receive the necessary training to perform their roles effectively.
- Monitoring and Measurement: Establish methods for monitoring and measuring processes, products, and services to ensure they meet quality requirements.
- Internal Audits: Conduct internal audits to assess the effectiveness of the QMS.
- Management Review: Top management should review the QMS regularly to ensure its continued suitability, adequacy, and effectiveness.
- Certification Audit: Engage a certification body to conduct an independent audit to assess compliance with ISO 9001.
- Certification: When the audit is successful, your organization can achieve ISO 9001 certification.
ISO 9001 certification demonstrates an organization’s commitment to quality and can enhance its reputation, improve customer satisfaction, and open up new business opportunities. Like ISO 27001, maintaining ISO 9001 certification requires ongoing effort and periodic audits to ensure continued compliance with the standard
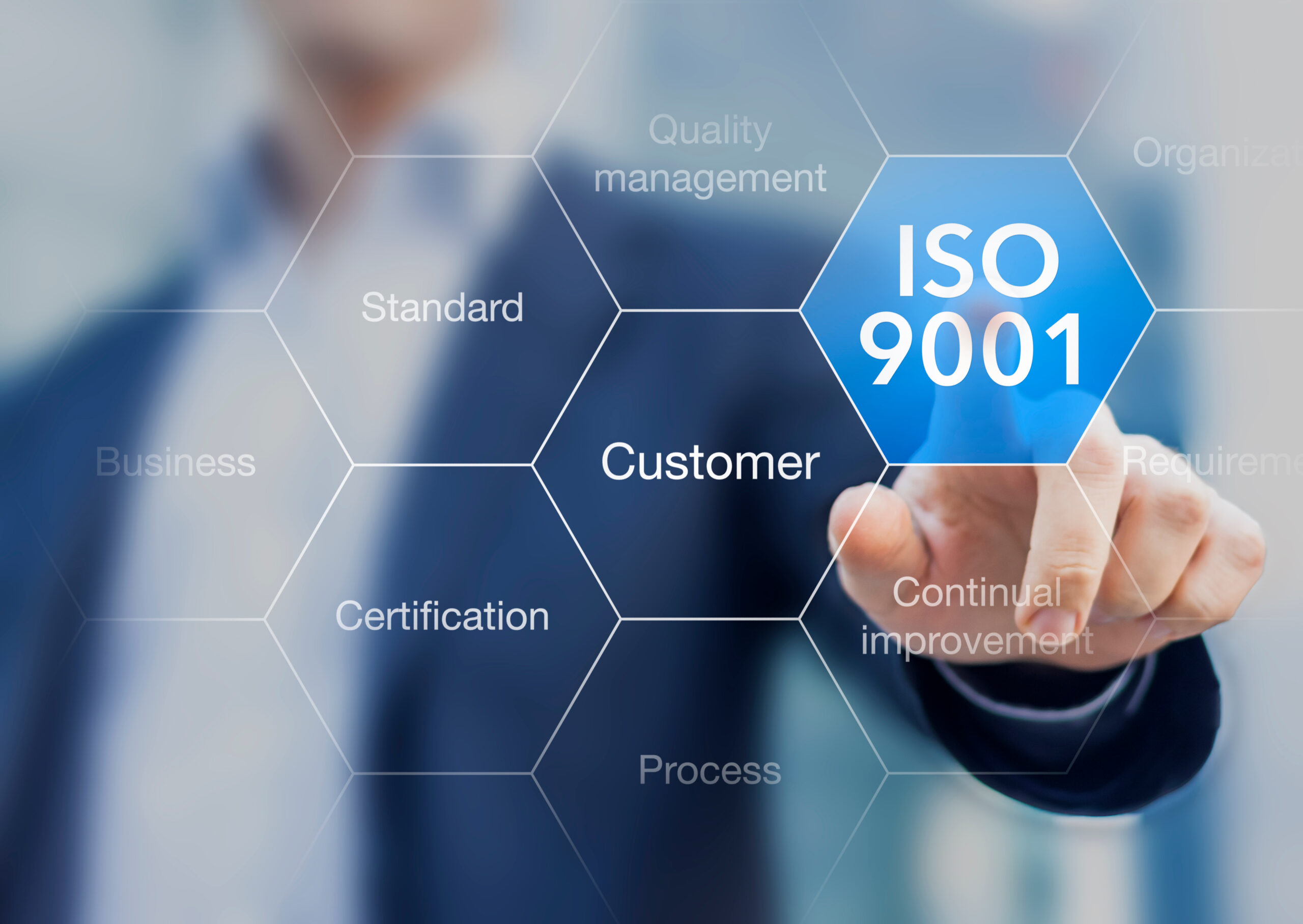
We are ISO 9001 Lead Auditor
Certified Exemplar Global , Certificate Number: IMS/LA/ACHF
We play a key role in evaluating and enhancing the quality management systems of organizations, helping them to meet ISO 9001 standards, achieve greater efficiency, and improve customer satisfaction.
We are recognized by certification bodies, consulting firms. We work within internal audit teams in organizations seeking ISO 9001 certification.
Our primary responsibilities and activities as an ISO 9001 lead auditor include:
Audit Planning
Conducting Audits
Document Review
On-Site Inspections
Nonconformity Identification
Reporting and Documentation
Follow-Up Audits
Communication
Compliance Assessment
Training and Development
Continuous Improvement
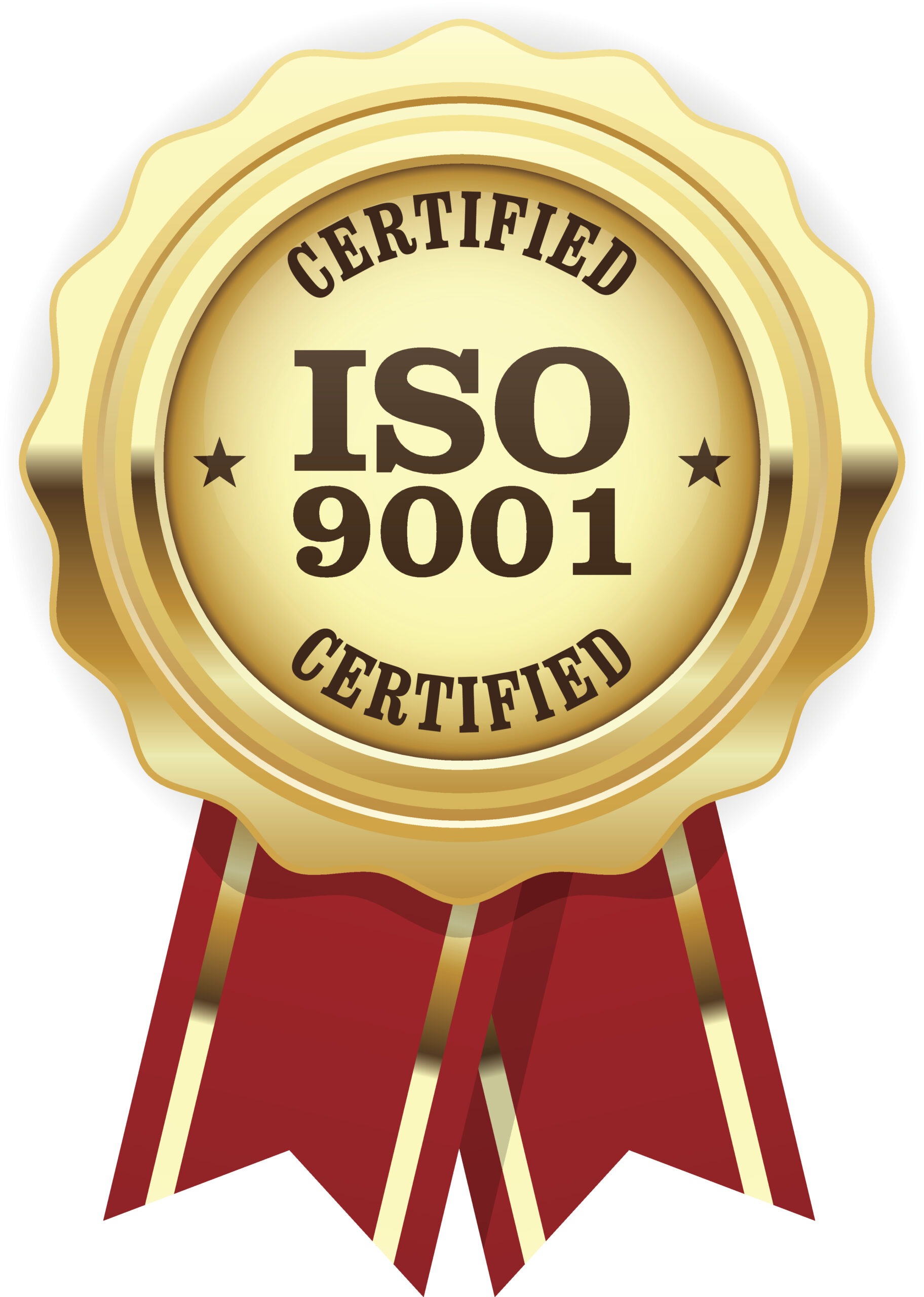
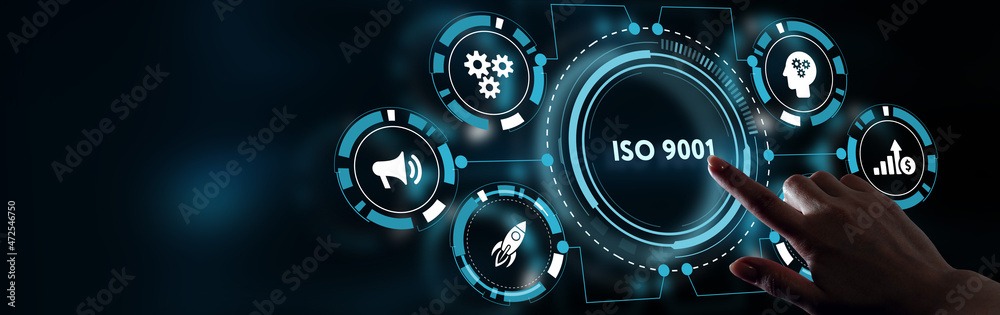